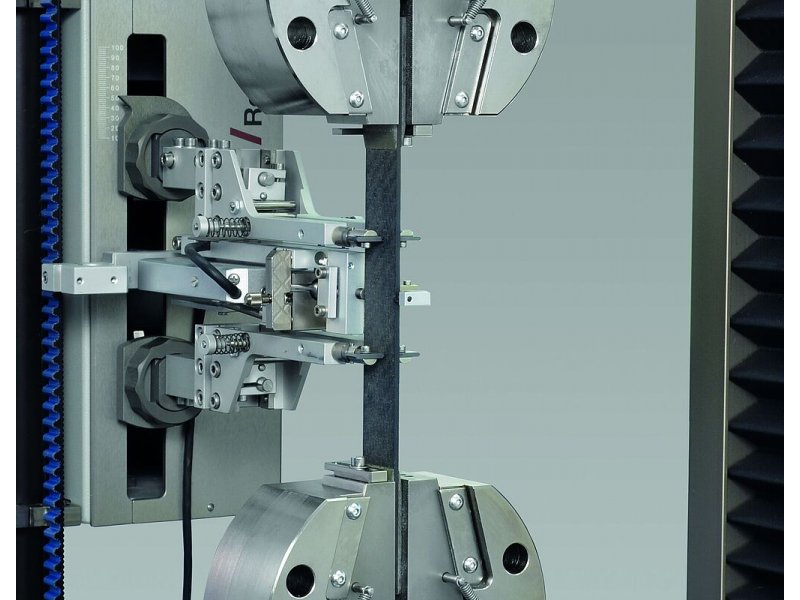
Kompozit Malzemelerin Üretiminde Kalite Kontrol Nasıl Sağlanır?
Kompozit Malzemelerin Üretiminde Kalite Kontrol Nasıl Sağlanır?
Kompozit malzemeler, yüksek mukavemet, düşük ağırlık ve korozyon direnci gibi özellikleri nedeniyle birçok endüstride tercih edilmektedir. Ancak bu üstün özelliklerin sağlanabilmesi için kompozit üretim süreçlerinde doğru kalite kontrol ve test yöntemlerinin uygulanması kritik öneme sahiptir. Peki, kompozit üretiminde kalite kontrol nasıl sağlanır ve hangi testler uygulanır?
1. Kompozit Malzemelerin Kalite Kontrolünde Neden Testler Gerekli?
Kompozit malzemelerin üretim süreçlerinde, kullanılan fiberlerin ve matrislerin doğru şekilde birleşimi ve istenilen mekanik özelliklerin elde edilmesi için çeşitli testler yapılır. Bu testler, malzemenin dayanıklılığını, mukavemetini ve çevresel faktörlere karşı direncini ölçer. Kalite kontrol aşamaları, üretimin her safhasında hataları önlemek ve güvenilir ürünler üretmek için tasarlanmıştır.
2. Kompozit Kalite Kontrolünde Kullanılan Temel Test Yöntemleri
a. Çekme Testi (Tensile Test)
Bu test, kompozit malzemelerin çekme mukavemetini ölçmek için kullanılır. Malzeme, çekme kuvvetine maruz bırakılarak kırılana kadar çekilir ve bu esnada malzemenin ne kadar dayanıklı olduğu belirlenir. Çekme testi, özellikle yüksek yük taşıyan uygulamalarda kompozitin mukavemetini kontrol etmek için kritiktir.
b. Bükme Testi (Flexural Test)
Bükme testi, kompozit malzemelerin esneklik ve eğilme mukavemetini değerlendiren bir yöntemdir. Bu testte malzeme, iki noktada desteklenir ve ortadan baskı uygulanarak eğilme dayanımı ölçülür. Bükme testleri, özellikle inşaat ve otomotiv sektörlerinde kompozit yapı elemanlarının güvenliğini sağlamak için kullanılır.
c. Darbe Dayanıklılık Testi (Impact Test)
Darbe testi, kompozit malzemelerin ani darbelere karşı dayanıklılığını ölçmek için yapılır. Bu testte, belirli bir ağırlık yüksek bir hızla malzemeye çarptırılır ve darbenin etkisi ölçülür. Bu yöntem, özellikle spor ekipmanları, savunma sanayi ve otomotiv sektörlerinde malzemelerin güvenilirliğini artırmak için kullanılır.
d. Isıl Dayanıklılık Testi (Thermal Testing)
Kompozit malzemeler, genellikle yüksek sıcaklıklara maruz kalabilecek uygulamalarda kullanıldığından, ısıl dayanıklılık testleri büyük önem taşır. Bu testlerde malzeme yüksek sıcaklıklara çıkarılarak boyutsal kararlılığı, mukavemeti ve ısıl genleşme davranışları ölçülür. Havacılık ve uzay teknolojilerinde bu testler hayati önemdedir.
e. Deformasyon Testleri (Deformation Tests)
Kompozitlerin fiziksel formunu ve şeklini ne kadar koruyabildiğini anlamak için yapılan deformasyon testleri, malzemeye uygulanan kuvvet altında yapısal değişikliklerin incelenmesini sağlar. Bu testler, özellikle ağır yük taşıyan yapısal elemanlarda malzemenin nasıl tepki verdiğini göstermek için kullanılır.
3. Ultrasonik Testler ile İçsel Kusurların Belirlenmesi
Ultrasonik testler, kompozit malzemelerin iç yapısındaki kusurların tespiti için kullanılan gelişmiş bir yöntemdir. Bu test, malzeme içerisine yüksek frekanslı ses dalgaları göndererek iç çatlaklar, boşluklar veya kusurların varlığını tespit eder. Özellikle uçak gövdeleri veya otomobil parçaları gibi kritik yapılarda içsel hataların tespiti için bu yöntem kullanılır.
4. TrimTech Composites’in Kalite Kontrol Süreçleri
TrimTech Composites olarak, kompozit üretim süreçlerimizde en yüksek kalite standartlarını sağlamak için kapsamlı testler ve kalite kontrol prosedürleri uyguluyoruz. Müşterilerimize sunduğumuz ürünlerin güvenilirliği, dayanıklılığı ve performansı için çekme, bükme, darbe ve ısıl dayanıklılık testlerinin yanı sıra ultrasonik testlerle içsel kusurları kontrol ediyoruz. Yüksek teknolojili laboratuvarlarımızda, kompozit malzemelerin her aşamada titizlikle test edilmesini sağlıyoruz.
5. Kalite Kontrol ve Test Yöntemlerinin Avantajları
Güvenilirlik: Kompozitlerin her uygulamada maksimum dayanıklılığı sağlaması, kullanıcıların güvenini kazanır.
Uzun Ömür: Kaliteli test süreçlerinden geçen kompozitler, uzun vadede kullanım ömrünü artırır.
Hata Azaltma: Üretim sırasında yapılan testler, potansiyel hataları önceden tespit ederek maliyetleri azaltır.