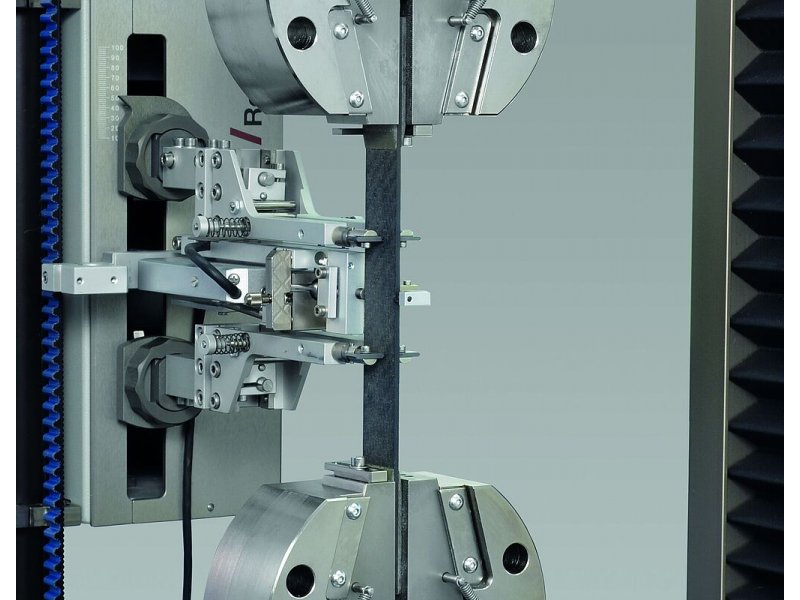
How to Ensure Quality Control in the Production of Composite Materials?
How to Ensure Quality Control in the Production of Composite Materials?
Composite materials are preferred in many industries due to their high strength, low weight and corrosion resistance. However, in order to ensure these superior properties, it is critical to apply the right quality control and testing methods in composite production processes. So, how is quality control ensured in composite production and which tests are applied?
1. Why Tests are Necessary for Quality Control of Composite Materials?
In the production processes of composite materials, various tests are performed to ensure the correct combination of the fibers and matrices used and to obtain the desired mechanical properties. These tests measure the material's durability, strength and resistance to environmental factors. The quality control stages are designed to prevent defects and produce reliable products at every stage of production.
2. Basic Test Methods Used in Composite Quality Control
a. Tensile Test
This test is used to measure the tensile strength of composite materials. The material is subjected to a tensile force and pulled until it breaks, at which time the strength of the material is determined. Tensile testing is critical to check the strength of the composite, especially in high load bearing applications.
b. Flexural Test
Bending test is a method to evaluate the flexibility and flexural strength of composite materials. In this test, the material is supported at two points and the bending strength is measured by applying pressure in the middle. Bending tests are used to ensure the safety of composite structural elements, especially in the construction and automotive sectors.
c. Impact Test
Impact testing is performed to measure the resistance of composite materials to sudden impacts. In this test, a certain weight is slammed into the material at a high speed and the impact of the impact is measured. This method is used to increase the reliability of materials, especially in sports equipment, defense industry and automotive sectors.
d. Thermal Testing
Since composite materials are often used in applications that can be exposed to high temperatures, thermal endurance tests are of great importance. In these tests, the material is exposed to high temperatures and its dimensional stability, strength and thermal expansion behavior are measured. These tests are vital in aviation and space technologies.
e. Deformation Tests
Deformation tests, which are performed to understand how long composites can retain their physical form and shape, allow the structural changes to be examined under the force applied to the material. These tests are used to show how the material reacts, especially in heavy load-bearing structural elements.
3. Identification of Intrinsic Defects with Ultrasonic Tests
Ultrasonic testing is an advanced method for the detection of defects in the internal structure of composite materials. This test detects the presence of internal cracks, voids or defects by sending high-frequency sound waves through the material. It is used to detect internal defects, especially in critical structures such as airframes or automobile parts.
4. TrimTech Composites' Quality Control Processes
At TrimTech Composites, we implement extensive testing and quality control procedures to ensure the highest quality standards in our composite manufacturing processes. We check for inherent defects through tensile, bending, impact and thermal strength tests, as well as ultrasonic testing to ensure the reliability, durability and performance of the products we provide to our customers. In our high-tech laboratories, we ensure that composite materials are rigorously tested at every stage.
5. Advantages of Quality Control and Testing Methods
Reliability The fact that composites provide maximum durability in every application gains the trust of users.
Long Life: Composites that undergo quality testing processes increase their lifespan in the long term.
Error Reduction: Testing during production reduces costs by identifying potential errors in advance.